看着崭新的规模化生产车间,繁忙的自动化作业现场,东莞市凯昶德电子科技股份有限公司陶瓷基板事业部总监吴朝晖博士长舒了一口气:“我们兑现了2015年年初对业界朋友的承诺”,吴博士笑着说:“去年年初,我们通过中国LED在线等业内媒体连续发表了2篇文章,对陶瓷大功率封装的技术现状及市场前景进行了乐观分析,承诺将在2015年第四季度实现陶瓷基板10万片/月的量产能力,并将W级功率型陶瓷基板未税价格下调至0.1元,这两点我们都实现了”。“当初做出公开承诺时,坦诚讲,我们是有点忐忑的,实现的过程也有些曲折,我们经历了市场从怀疑到接受的艰难过程,也经历了需求井喷时产能不足、供应不及时的被动局面,也曾出现过带来重大损失的品质事故,我们承担了责任,也吸取了教训。”吴博士说:“市场需求爆发的时间节点比我们的预期早了点,我们的扩产略显滞后,出现了供不应求的局面,甚至不得不推掉部分订单,招致了不少客户的抱怨,好在一切都挺过了,现在凯昶德陶瓷基板在业内已有相当知名度,其性价比相比台湾同类产品优势明显,同时,2期10万片产线的顺利投产将极大缓解当前国内市场供不应求的局面。”
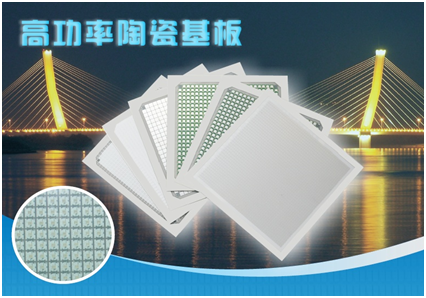
“凯昶德推出的薄膜线路陶瓷基板,其制造工艺与传统陶瓷基板有很大不同”,吴博士说:“传统LED陶瓷基板主要为低温共烧(LTCC)陶瓷基板及厚膜丝印陶瓷基板,这两种基板均采用厚膜印刷技术完成线路制作,线路表面较为粗糙(Ra约为1~3um),对位不精准,其工艺解析度较为受限,并不能适应当前高功率LED倒装/共晶封装的要求。而凯昶德自行研发的薄膜线路陶瓷基板,是一种结合薄膜制程与电镀制程技术,在高导热氧化铝或氮化铝陶瓷板上以影像转移方式制作金属线路,线路解析度可达50um,表面粗糙度小于0.3um、线路对位精准度误差值仅±1%,具备了高导热系数、高线路精准度、高表面平整度的特性,非常适用于LED倒装/共晶工艺,是最适合高功率且小尺寸LED发展的陶瓷封装基板。”
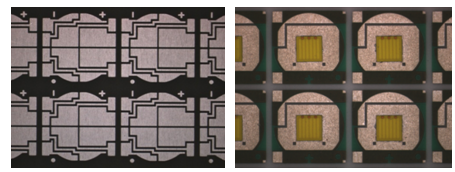
图 凯昶德陶瓷基板线路图及共晶封装图
“我们从2012开始研发立项,到现在已整整做了四年。”谈到这个项目的产业化历程,吴博士娓娓道来:“当初业内与我们同时开发的企业有近10家,而现在,真正实现规模化量产能力的只有我们一家。”,“回顾我们的研发历程,我一直都很庆幸立项当初我们对技术难度的“懵懂无知”,这也许就是所谓的“无知者无畏”吧”,吴博士感叹的说:“这个项目的技术难度是超过我们最初预期的,好在四年我们都坚持了下来,解决了核心问题,并进行了相关专利布局,现在我们共申请了6项发明专利,其中4项已经授权,实现了从设备到方法的全覆盖”。
薄膜线路陶瓷基板的核心技术可以归纳为两点,其一是陶瓷基板的薄膜金属化技术,其二是实现双面布线垂直互连的穿孔电镀技术。这两项核心技术在各自领域似乎并不陌生,比如薄膜金属化经常应用于半导体器件,而穿孔电镀技术则在PCB行业相当成熟。“似乎难度并不高”,吴博士笑着说:“立项当初我们也是这么认为的,自己做不了就找厂家代工嘛,可等我们一开始做,发现完全不一样,代工厂根本做不好也做不了,后来我们不得不全工序自己做。”
“我可以用“神似而形不似”来概括陶瓷基板薄膜金属化与半导体领域的区别,它们金属化的原理是一样的,都是采用真空溅射的原理,且需要过渡层及种子层实现陶瓷-金属间的低应力及高结合力,但要实现大规模化量产,陶瓷基板薄膜金属化设备的构造与半导体行业设备完全不同,半导体行业这类设备都是独立的单腔式,制作精密,价格昂贵,生产效率低,是不能适用于低成本陶瓷基板规模化生产要求的,好在我在博士期间接触过单腔式的真空镀膜设备,对金属化原理有较深入的研究,同时公司有一个高水平的自动化团队,我们联合攻关了一年,终于开发出一套高性价比的连续式磁控溅射镀膜系统,再经过半年的改装调试,现在无论是自动化操作性、生产产能,还是镀膜品质,都完全满足陶瓷基板薄膜金属化的要求”。“当初我们进行设备调研时,对方报价一千多万一台,差点让我们直接放弃这个项目,我们自行开发,为项目经费省下了很大一笔钱,要实现低成本,要从节省设备投入开始。”
“至于另一个核心技术穿孔电镀,我可以反过来用“形似而神不似”来概括它与现有PCB行业技术的区别,那就是设备外形很像,但技术原理不同,比如穿孔,PCB行业用机械钻孔,而陶瓷基板采用的是高精密激光钻孔;再比如电镀,PCB行业是电镀填盲孔或者空心孔,而陶瓷基板需要电镀填实心的贯穿孔,其物料与工艺与PCB行业完全不同,这也是代工厂做不好做不了的原因。”
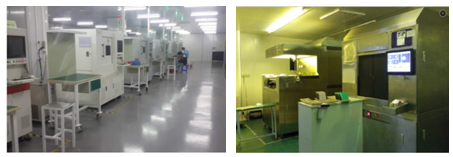
图 凯昶德陶瓷基板激光加工车间及黄光微影车间一览
激光穿孔精度高,速度快,孔型完整,热影响区小,是陶瓷基板制造流程中第一道,也是至关重要的核心工序之一。吴博士说:“资金不能省的地方一定不要省,激光加工品质非常重要,设备100多万一台,且要实现规模化生产,必须得上10台以上,仅这一道工序,就要至少上千万的投资,实力弱的企业是无法上量的;而电镀填孔对工艺的管控要求非常高,工艺不匹配会导致附着力不佳、填孔不良等质量问题,给客户带来很大的品质隐患,因此,无论从资金壁垒还是从技术壁垒来看,陶瓷基板都是门槛较高的产业。”
谈到陶瓷基板的市场前景,吴博士是谨慎乐观的。“陶瓷基板在LED封装行业属于细分市场,根本谈不上能一统天下,但由于其特有的优势,仍在高附加值的封装市场牢牢占据相当份额。”
“从需求端来看,整个LED行业陶瓷基板的月需求量大约在50万片左右,市场规模每年不到10亿元人民币,客户集中度非常高,主要包括科锐、欧司朗、飞利浦、首尔、日亚等国际大厂,以及晶能、德豪、鸿利等国内上市公司,其中科锐需求最大,约占总需求的1/3左右,其它国际大厂的总需求共占1/3,国内厂家的总需求占最后的1/3。”
“国内大厂的需求还是最近2年才培育起来的,我在去年的文章中也提到过,2011年大陆上马的陶瓷封装线有20多条,但现在坚持下来的也就晶能、德豪、鸿利等寥寥数家,这要得益于这几家企业拥有各自的看家本领,比如晶能的硅衬底芯片、德豪的倒装芯片、鸿利的车灯布局等。现在这几家公司陶瓷封装产能已逐步扩大,大有迎头赶上国际大厂的趋势,相应地,对国产低成本陶瓷基板的需求愈来愈大,而我们,刚好赶上了这个时机。”“一个新产品,从研发到推向市场,节奏的把握很重要,节奏过快很容易成烈士,太慢,那就是起个大早赶个晚集,会错过收回投资成本的最佳时间窗口,毕竟投资是要讲回报的。”
“从陶瓷基板的供应端来看,目前的局面是一家独大,”吴博士接着分析道:“在我们实现规模化量产之前,陶瓷基板由台湾地区数家企业垄断,其中同欣最大,占了80%的市场份额,其余的市场份额被大毅、立诚、瑷司柏等企业瓜分,我们现在推出的10万片月产能,满产后也仅占整个市场份额的20%左右,暂时不会对当前供应格局带来挑战,但陶瓷基板的客户群绝大部分在大陆,凯昶德陶瓷基板占据着明显的地域及成本优势,肯定会改变现有的供应格局。”吴博士信心满满的说道,“这只是时间问题。”
除了传统的户外照明、强光手电筒等市场,一些新兴市场在2015年已逐步成熟并形成规模需求,比较典型的有车用LED、手机闪光灯、紫外 LED固化、红外LED安防、植物照明等市场领域,使陶瓷基板市场无论是渗透率还是容量都在增加。以车用LED为例,根据LEDinside最新2016 LED供需市场趋势报告显示,车外照明用LED市场产值至2020年可望来到22.9亿美金,年复合成长率为8%。手机闪光灯方面,智慧型手机对高像素的追求使得原来1颗闪光灯的标配变成了2-3颗,到2018年全球手机闪光灯出货量预计将达20.43亿颗。紫外LED市场也是如此,由于技术门坎较高,产品单价较一般LED高出数十倍,属于高毛利市场,庞大产值已吸引众多厂商争相投入。
“这些新兴市场不断释放出利好消息,对陶瓷基板的需求格局也产生了重大影响,逐渐催生出第四大目标客户群,那就是深圳一批从传统SMD贴片式封装转型过来的企业,对此,不得不佩服他们市场嗅觉的灵敏性和转型的果断性,当然,也和整个广东地区相关芯片、基板、封装技术、配套设备的日渐成熟有关。”吴博士饶有兴趣的说:“这些企业是从2015年开始陆续出现的,大部分从被卖成白菜价的贴片式封装转型过来,每个企业仅专注于某个细分市场,比如有专门做手电筒灯的,专门做车灯的,专门做UV灯的,每家企业规模不大,但数量较多,总体需求不容小觑,在未来3年内,极有望成长为继前三大客户群之后的第四大客户群,形成四分天下的需求格局,而且,这个市场目前完全由我们占有。”
“其实,陶瓷基板的用途远不止LED这个行业”,吴博士继续道:“陶瓷基板产业涉及精细陶瓷制备、薄膜金属化、黄光微影、激光成型、电化学镀、光学模拟、微电子焊接等多领域技术,产品在功率型发射器、光伏器件,IGBT模块,功率型晶闸管、谐振器基座、半导体封装载板等大功率光电及半导体器件领域有广泛用途。”“比如采用陶瓷基板封装的功率型IGBT模块,主要应用于家电用功率变频器、新能源汽车用逆变器、USP电源、电动汽车充电桩等电力电子领域。近年受我国高铁、动车、地铁等轨道交通、新能源汽车、光伏发电、高压输变电网、无线发射基站等领域投资规模提振的影响,这些领域犹如2000年初的LED市场,正处于蓬勃兴起的阶段,市场前景值得期待”。“这些新领域对陶瓷基板的需求估计有上百亿的规模,比LED行业大得多,陶瓷基板真的大有可为,目前我们已经着手进行相关市场开拓和专利布局。”
任何一个好的行业不会没有竞争对手,机会大家都可以看到,一家独大的局面不会维持太久,陶瓷基板也不例外,凯昶德的陶瓷基板在大陆具备先发优势,但这种先发优势不是偶然的,这一方面归益于公司掌舵人吴乐海董事长对市场前景敏锐的洞察力、不轻言放弃的执着以及持续不断的资金支持,另一方面要归结于4年来技术团队的刻苦攻关和坚持不懈。
针对可能出现的大陆竞争对手,吴博士有自己的看法:“四年前市场前景可没现在这么乐观,当时COB及EMC刚刚兴起,对高功率陶瓷封装形成夹击局面,业内很多人是不看好陶瓷基板项目的,但吴董事长坚持认为,陶瓷基板有其特有的技术优势,应该具有顽强的生命力,而且它属于一个全新的技术平台,做得好可以向电力电子、光电半导体器件等领域渗透,对公司的转型升级具有重大意义,因此拍板一定要搞,当时如果没有吴董事长的一再坚持,可能我们这个团队早就解散了。”当谈到自己的团队时,吴博士充满自豪:”这个项目最重要的是团队培养,设备可以用钱买,但相关的设计规范、作业指引、工艺流程、品质标准、管理制度等用钱是买不到的,100多项文件,都得靠人去撰写、去培训、去执行,且非朝夕之功,需要长时间的沉淀积累;国内没有现成的人才可挖,都是通过内部选拔结合外部引进慢慢培养出来的,也许团队才是我们最宝贵的财富,最大的核心竞争力”。
“现在市场前景普遍看好,我们也关注到有几家企业正在开发,因此预计2017年会有竞争对手出现,对此我们已经做好充分的准备,2016年我们定义为成本下降年,随着国内配套的成熟,我们制程良率的提升,规模化效应的显现,以及高密度布板方案的推广,2016年陶瓷基板成本肯定会进一步下降,以3535为例,单颗售价在下半年肯定会降至0.1元以内,直逼EMC价格。”
“没有对手的江湖是孤独的,我们更乐意看到竞争对手出现,这样我们才能不断超越自己,发扬工匠精神,把性能做到极致,把成本做到极致,把服务做到极致,使客户收益,让陶瓷封装这个产业继续散发独特的魅力,推动行业的整体进步。”吴博士意味深长的说。